TECH DIVE: Moment of truth for Ceramic Membranes
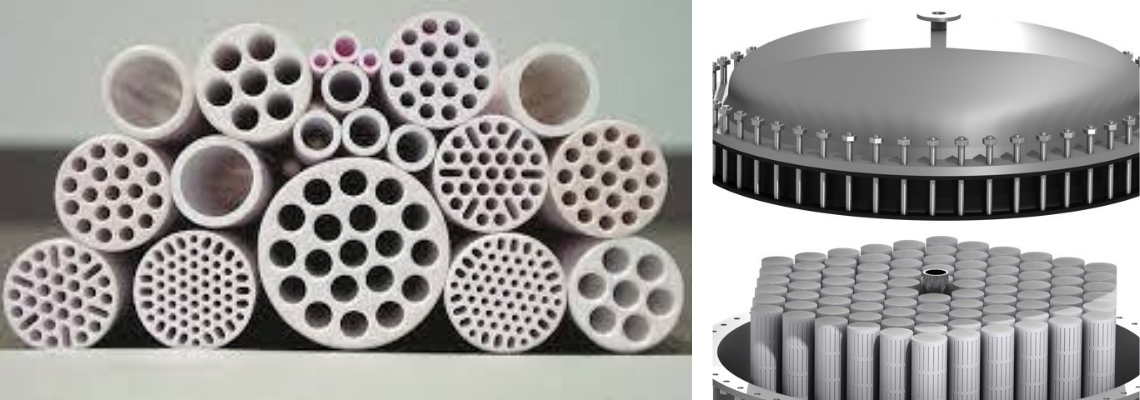
Is history repeating itself?
Ceramic membranes have been around for a while but several factors such as higher costs and a lack of industry ambassadors have stunted their potential progression into the utility sector.
Yet, recent developments in the ceramic membranes space have led some industry thought leaders to draw comparisons to the rise and eventual domination of polymeric membranes.
Which raises a question: is this the moment of truth for ceramics membranes?
Deja-vu
Before we can look forward, we need to look back at not only the history of ceramic membranes but first to its cousin, the polymeric membrane.
Polymeric membranes have been the go-to membrane of choice for the utility sector for the past three decades, ever since they were first considered for use in drinking water in the mid-90s.
Source: Applied Biomimetic
However, they were not without their sceptics as Dr Graeme Pearce, renowned membrane expert and principal at Membrane Consultancy Associates, explains:
"Polymerics took the world by storm [in the mid-1990s]. When polymeric membranes were starting to be considered in drinking water, there were only a few product champions. Scepticisms started to grow about whether polymerics would last, whether they would break and whether there would be integrity issues."
Ultimately, it would be the integrity issues that these sceptics would focus on after a small number of plants had issues.
"Polymerics took the world by storm.”
"They had their worst fears realised with integrity problems,” adds Dr Pearce. "Normally, I give a figure of 85 per cent of polymeric plants which are successful and do not have issues
“The other 15 per cent are made up of five per cent which could be deemed to be moderately successful, another five per cent causing operational headaches and the final five per cent having massive issues with their facilities."
The sector is now experiencing a sense of deja-vu with ceramic membranes. Scepticisms around ceramics existed when they were being considered for drinking water and use in utilities.
This time the scepticisms are around the perceived higher cost of ceramic membranes. Is this about to change?
Perfect storm conditions
"The perfect storm conditions have arrived," says Dr Pearce, optimistically.
There have been a number of blockers stopping ceramic membranes from taking the water sector by storm, from higher price points compared to polymeric membranes to a largely unconvinced utility sector not wanting to be the first through the breach.
Previously, ceramics have been priced out of the utility market in favour of polymeric membranes. However, due to the nature of ceramics and the benefits they offer, an equalisation is occurring.
Source: The American Ceramic Society
"The prices are levelling out,” adds Dr Pearce. “The higher price of the ceramic tends to balance out with the higher level of performance. I think ceramic membranes and polymeric membranes are on a level playing field in comparison."
Ceramic membranes, for their higher price point, offer utilities greater longevity than polymeric membranes and are able to handle significantly higher fluxes. Previously, ceramic membranes would not have been considered as an option by water utilities. Today we are starting to see them be considered and even in some cases, specified as the only option.
For example, back in 2020, UK water utility South West Water’s Mayflower Water Treatment Works at Roborough, Plymouth, ungraded its plant to use suspended ion exchange, inline coagulation and ceramic membrane microfiltration.
"The perfect storm conditions have arrived."
The utility said this move was to produce more water, more efficiently and at a lower cost than traditional technology.
The new treatment processes at Mayflower were designed and developed by Dutch water technology company PWNT, before its acquisition by Nijhuis Saur Industries.
"It's taken a while for the commercial position to really become settled so that people have the confidence," adds Dr Pearce.
"You want more than one credible drinking water supplier for example. You've got to have two. Otherwise, the drinking water industry in the UK and anywhere else will not accept a bid from one supplier in a particular category.
"They want a critical mass of ceramic suppliers."
Taking ownership of the ceramic poster child
Aquatech recently covered the acquisition of PWNT by Nijhuis Saur Industries and its ambition to elevate the ceramics marketplace.
Originally spun out of Dutch drinking water utility PWN, PWNT has been regarded as the poster child for ceramic membranes, particularly in showcasing how they can be applied, at scale, to utility drinking water applications.
Speaking on the acquisition, Dr Pearce said: "I think Nijhuis will be aggressive with it, they will really move ceramics forward."
PWNT developed a way to reduce the price of ceramic membranes by grouping together a large number of ceramic membrane modules, stacked together and housed within one large vessel.
“Nijhuis will be aggressive with it, they will really move ceramics forward."
Called the CeraMac® it has engineered a filtration process based on combining up to 90 ceramic membrane elements into one vessel - reducing the price and the footprint.
Source: PWNT Technologies
PWNT say its CeraMac is energy efficient, requires little maintenance, and is able to backwash at a pressure of five bar which only requires a few seconds of downtime.
This unique method allowed PWNT to sell the CeraMac as a whole system and reduce the price, as opposed to individual modules.
"If you look at innovation in drinking water, we have much technology to get to that market and also, with our capabilities built up around industrial, we can bring solutions to the market much faster,” said Menno Holterman, CEO of Nijhuis Saur Industries.
Under Holterman’s watch, the acquisition of PWNT and its ceramic membranes technology will enable the company to make a stronger play into the drinking water market.
This is not the only method being used in the sector and PWNT's dedication has led to the formation of other ceramic membrane companies entering the market.
The segmented approach
Formed in 2012 to develop and commercialise ceramic ultrafiltration technology, Nanostone Water released its first ceramic membrane solution for commercial sale in 2017.
In contrast to PWNT, Nanostone Water decided not to group all its membranes into one vessel, but instead to position its modules on a rack to allow for more flexibility and enable retrofitting existing vertical polymeric microfiltration/nanofiltration (MF/UF) systems.
Nanostone Water's ceramic membranes are ceramic sheets that are configured into a patented segmented monolith design.
"Right now for the first time, ceramics are being considered from the start.”
The water technology company says its design allows for unrestricted permeate flow out of the ceramic material along the entire length of the module, eliminating flow restrictions and unnecessary pressure drops.
Each monolith is integrated into a housing to provide what Nanostone Water says is an easy-to-use and corrosion-free module.
With a backwash pressure of up to seven bars, the module can be retrofitted to all major racks as well as be deployed in a wide range of greenfield system designs.
"We are at the beginning of the perfect storm for us," said Gilbert Galjaard, chief process at Nanostone Water.
"There is outdated equipment, especially in the UK. Equipment that needs to be replaced, or equipment that is facing challenges.
"Right now, for the first time, ceramics are being considered from the start where before we would be chasing failing installations," Galjaard went on to say.
The decision to go with a modular system comes down to how Nanostone Water wants to be positioned in the market.
Source: Nanostone Water
"Nobody wants to be the first," a Michael Shaw, director of product management at Nanostone Water.
"The ability to retrofit was a design choice we made for water utilities to make it easier to take a chance on our technology. But no one wants to be first, and that's hard work.
"Our design has enabled us to quickly go into sizable commercial plants that are struggling today and replace the modules and solve their problems immediately.
"Now that we have traction here, we bring our solution to seawater desalination projects by referencing what we've done in surface water and industrial applications. Desalination pre-treatment has unique challenges that ceramic technology is uniquely suited to address" said Shaw.
Positioning themselves as a quick solution to water treatment without an expensive plant redesign will be appealing to many water utilities.
A good example of this is the retrofit at the Rapid Valley Sanitary District, in South Dakota, where the municipality was not able to provide its community with the required three million gallons per day.
Nanostone Water was able to retrofit two racks of its ceramic membranes to help restore the municipality’s water output.
3D printing Separonics
Ever heard of Separonics™?
Thought not, as until recently it was not a widely known term to the point where creators Evove, formerly G2O Water Technologies, came up with a definition for the newest player in ceramics.
By definition, a separonic is a transforming membrane that has the capability to recycle water and recover valuable resources at a reduced price point.
However, it is with its Separonics that the UK technology company is aiming to disassociate itself with the preconceptions surrounding ceramic membranes.
"A membrane is perceived in the marketplace as being something which can work, but it's troublesome. You need large plants to be able to make the economics work,” says Chris Wyres, CEO of Evove.
“They [membranes] foul-up. You need experts. They only last a few years if you're lucky, sometimes less. Ceramics cost a lot of money, energy, and chemicals. That's the perception in the marketplace."
"Separonics are our answer to the dirty word, membrane."
The company is turning to a technology that never fails to get the water sector excited, if a little sceptical - 3D printing.
Source: Unsplash – large scale 3D printing
This new generation of Separonics is being positioned as “precisely engineered, 3D printed, filtration and separation technology” and a “physical barrier that will be designed bespoke for any application or customer”.
In this context, 3D printing is not referring to a small device that sits on a desk and takes two days to print a whistle. Instead, it will be 3D, industrial printing at scale.
"We will be able to print at full scale, eight-inch wide, 1.8 metres long, whatever length really, it doesn't really matter," says Wyres.
"All you're doing is stacking layers on top of layers. So you just need a building height. We will be able to print up to 12, 15 inches, it doesn't matter. It's modular and scalable.
"The key is that we will be able to print features and structures which conventional manufacturing can't, and using high-performance computing and AI to optimise those designs for specific applications."
At the end of 2021, Evove signed a signed a Joint Development Agreement with Meta Additive to produce an advanced additive manufacturing solution to 3D print its ceramic Separonic membranes, with plans to deploy in 2023.
This project, according to Evove, will seed its solution into the market and create a blueprint to scale up.
Through this approach, the company believes it can reduce the manufacturing cost of ceramic membranes by at least 60 per cent.
Flat sheets
Flat sheet ceramic membranes have been around since 1993 but in 2016, German company Cerafiltec was founded to see how far the technology could be pushed.
Cerafiltec's ceramic flat sheet membrane works with a filter active layer on the outside of the membrane. Suspended solids are rejected on the membrane surface and form a cake layer, while clean water is passing through the membrane body and is collected at both end caps.
Water from each single plate is collected inside the module housing and transported to the header set through four filtered water channels integrated into both module housing sides.
These filtration towers are submerged in a tank, known as a filtration train, which contains the feed water with all the towers connected at the top with a single header pipe.
The filtered water is transported through the header set of each tower to the top and from there through the common header pipe to the tank outside where a filtration pump is connected to transfer the clean water to the filtered water tank.
Flat sheets are a different approach to ceramics than what PWNT is doing and has different strengths. Ceramic plates are cheaper compared to traditional ceramics technologies which make them an attractive offer to utilities that are unsure whether to take the plunge.
Previously, flat sheets have not been considered an option for drinking water but instead found success in seawater reverse osmosis pre-treatment in the desalination industry.
Tides are changing
We started this Tech Dive with a question: is history repeating itself?
Looking at the current market, new players and the emerging technology being leveraged and explored, there are a lot of similarities that can be drawn between the acceptance of polymeric and ceramic membranes for municipal treatment.
From scepticism over whether ceramics are worth the extra cost, to concerns about whether they are up to the task of the utility market, inevitably, critics will still exist. However, with more and more utilities now considering ceramics, progress is visible. All that remains to be seen is who will take the leap and be the next ceramic membrane leaders.
Related content
- Why we bought PWNT: Holterman strengthens Dutch tech powerhouse with ceramics
- The perfect storm for ceramic membranes
- Membranes tech dive: seeking the holy grail
Share your water technology stories with us
Do you have an innovation, research results or an other interesting topic you would like to share with the international water technology industry? The Aquatech website and social media channels are a great platform to showcase your stories!
Please contact our Sr Brand Marketing Manager Annelie Koomen.
Are you an Aquatech exhibitor?
Make sure you add your latest press releases to your Company Profile in the Exhibitor Portal for free exposure.