Purpose-built plant will recover phosphorous from sewage sludge
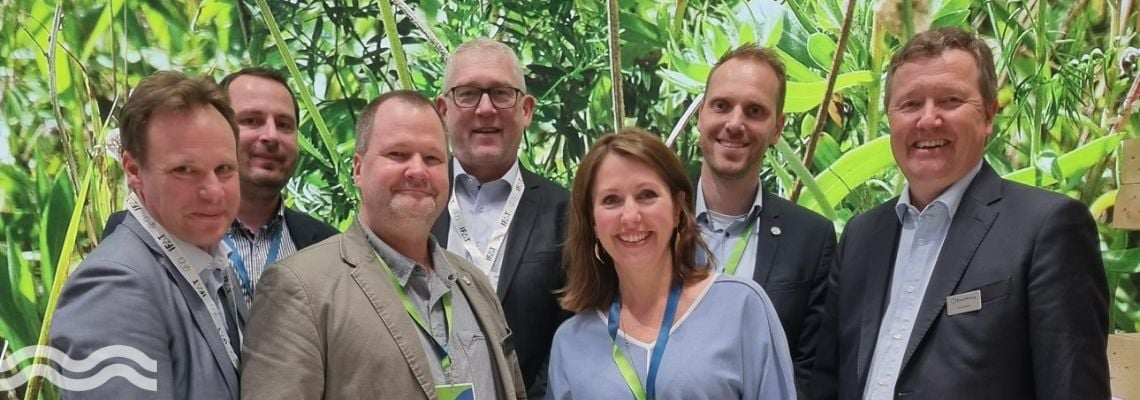
Gelsenwasser AG and EasyMining will establish the world’s first phosphorous recovery plant that utilises Ash2Phos technology. The plant will recover phosphorous from sewage sludge ash at the plant, which is scheduled to begin operations in 2027.
Using sludge to create a sustainable phosphorous source
The two companies were among the founding members of the Sauberer Phosphor 2029 (Clean Phosphorus) initiative that saw a number of companies in Germany come together to champion new phosphorous recovery and recycling processes.
Together, Gelsenwasser AG and EasyMining have created Phosphorgewinnung Schkopau GmbH (PGS), a joint venture that will deliver the plant, using EasyMining’s Ash2Phos technology.
The plant has a targeted capacity of 30,000 tonnes per year, the equivalent of 10 per cent of Germany’s current total sewage sludge ash volume.
Christian Kabbe, managing director, EasyMining Germany, said: “If we are serious about creating a sustainable society, we need to use the resources we already have, over and over again.
She added: “Therefore, we are glad that within this investment we will be able to unlock the potential of sewage sludge ash as a domestic and circular phosphorus source.”
How does Ash2Phos technology work?
The Ash2Phos process happens in three stages: a first acidic step, a second alkaline step (where intermediate products are produced), and finally a conversion step where the intermediates are processed into final products.
The process can achieve a 90-95 per cent extraction rate of phosphorous from the ash of incinerated sewage sludge. It also recovers 60-80 per cent aluminium and 10-20 per cent iron.
The successive chemical reactions also separate out unwanted and potentially harmful elements, e.g. cadmium, for safe disposal, so that these are not released into the environment, for example, through fertiliser products.
The high-grade phosphorus extracted can be used as slow-release fertiliser, animal feed phosphate, or can be further processed into conventional fertilisers.
In addition to phosphorous recovery, the process has the benefit of producing usable by-products, including: ferric chloride, sodium aluminate, and sand.
Martin Braunersreuther, managing director at Phosphorgewinnung Schkopau, said: “As members of the 'Clean Phosphorus 2029' initiative, we are steadfast in our commitment to fostering environmentally friendly phosphorus recovery processes.
He added: “Through collaborative endeavours, we aim to realise defined targets for phosphorus recovery, while simultaneously advancing sustainable practices and enhancing resource efficiency.”