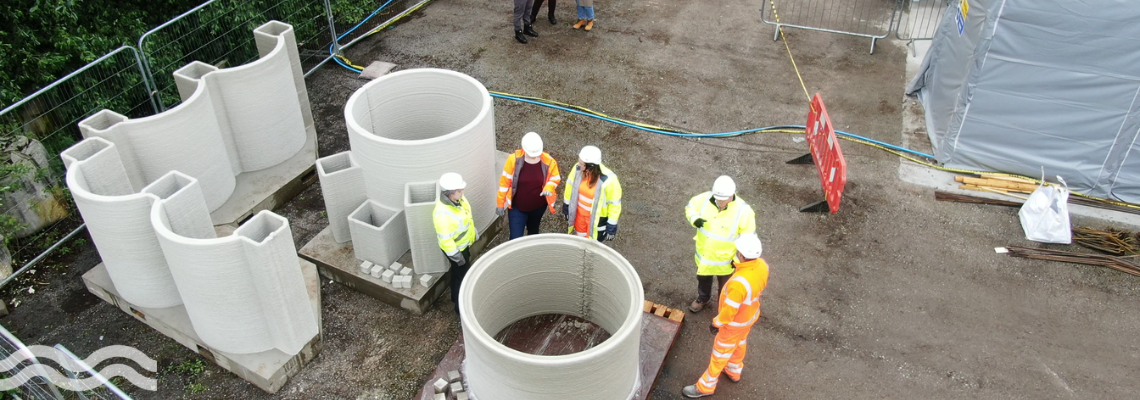
In the UK, water industry components are being printed in 3D concrete in a matter of hours following investment from the Ofwat Innovation Fund.
Tech innovation could have huge benefits to water utilities
A range of equipment is being produced, including combined sewer overflow (CSO) chambers, which will play a vital role in helping to reduce spills from the sewer network. The benefits of these 3D concrete printed components are being trialled at the Wigan Wastewater Treatment Works, a United Utilities hub.
The northwest utility is working with tech innovators ChangeMaker 3D, Manchester Metropolitan University and Scottish Water to develop the ‘Water Industry Printfrastructure’ technology following an award of almost €2 million. The robotic technology and materials are being provided by CyBe robotics.
United Utilities’ head of innovation Kieran Brocklebank said: “We’ve been working closely with ChangeMaker 3D for three years during which time the processes have been honed. To finally see a production line of assets being printed is a huge step forward and one we were all excited to see.
“We are about to embark on our biggest ever capital investment programme and have tight deadlines to meet. Digital technologies such as 3D construction printing will play an important role in driving efficient construction and helping us meet our Net Zero goals for carbon.”
copy
Three years in development
The project began in 2021 when ChangeMaker 3D was selected to take part in United Utilities’ Innovation Lab. In 2022, the two companies produced a wastewater chamber for use at one of United Utilities test facilities in Cheshire. For the past two years, the process, technology and products have been tested to demonstrate their suitability for wider use.
Four hours from start to finish
The printing process for a CSO chamber lasts for just over an hour. The chambers are then left for a minimum of three hours to dry – this compares to two days needed using traditional methods. Some small items can be printed in as a little as 45 minutes.
The benefits of 3D printed water infrastructure
As well as the time savings compared to traditional methods, the process delivers safety benefits in terms of construction methods, and an estimated 50 per cent carbon saving.
Natalie Wadley, co-founder and CEO of ChangeMaker 3D, said: “The water industry has a major challenge, and we can’t afford to stand still. This project really shows the solution, as well as the adoption and impact of the technology at large. We’ve really built a transparent and honest relationship with United Utilities which has enabled us to step through this journey together, face this head on and remove the barriers as they appear.”
3D printing has been used in other water tech projects, for example, when producing membrane spacers.
Sharing the technology’s potential
The 3D printing hub allows concrete assets to be readied in hours rather than days. The project partners are using the Wigan plant to demonstrate the process to other water companies, construction partners and even other industries. Some of the products being produced at the hub will be trialled by Scottish Water.
Ian Watt, Scottish Water’s Beyond Net Zero Delivery Manager added: “By thinking ‘clever’ and adapting traditional methods to modern needs and aspirations we can build on our successes and 3D concrete printing is certainly a method that could work very well for us.”
As well as 3D concrete printing, the Ofwat-backed project will also see products being printed using polymer materials.
Share your water technology stories with us
Do you have an innovation, research results or an other interesting topic you would like to share with the international water technology industry? The Aquatech website and social media channels are a great platform to showcase your stories!
Please contact our Sr Brand Marketing Manager Annelie Koomen.
Are you an Aquatech exhibitor?
Make sure you add your latest press releases to your Company Profile in the Exhibitor Portal for free exposure.