Counter flow membranes drive lithium production efficiencies
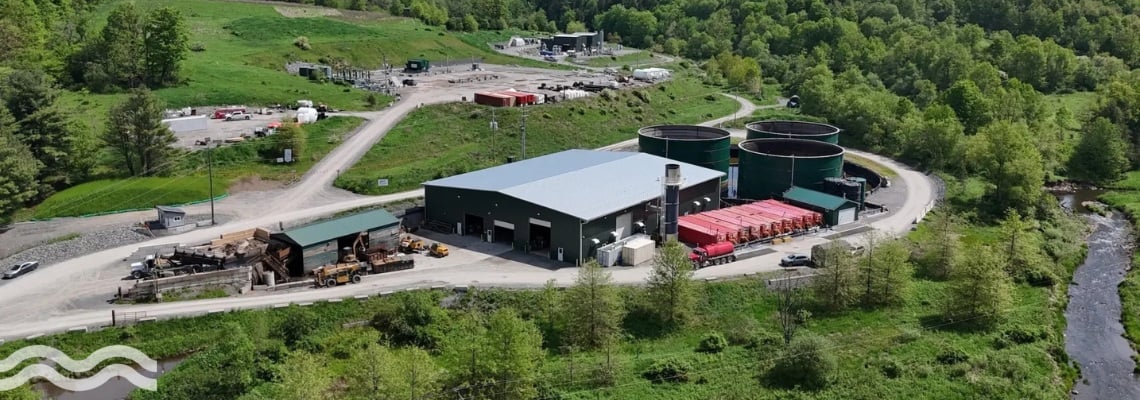
Lithium extraction is being made more efficient by counterflow reverse osmosis (CRFO) membranes at what has been described as the world’s first fully integrated production facility.
Where is the facility and who is building it?
Water and resource recovery specialist Gradiant is designing and building a commercial lithium production facility in the Marcellus Shale Formation of Pennsylvania, through its offshoot company alkaLi. The ‘vertically integrated model’ avoids permitting and ownership issues that cause delays in other mineral extraction projects because all equipment, land, water and mineral rights, as well as all permits are owned by alkaLi. The facility will help to secure lithium supplies in the US.
The company claims that the site will be the world’s first to extract, concentrate, and convert lithium in a fully integrated, end-to-end process from oilfield produced water.
The plant is expected to begin operating commercially in 2026 and will use alkaLi’s EC2 platform, which has proved during testing that it is capable of achieving 97 per cent lithium recovery from produced water and 99.5 per cent purity for battery-grade lithium carbonate.
How is lithium extracted from oilfield produced water
The company’s patented EC2 process combines Direct Lithium Extraction (DLE), concentration, and final conversion into a single streamlined system.
According to the company, compared to conventional methods, EC² offers:
- Up to 50 per cent lower capital and operating costs
- Modular, pre-engineered systems for rapid global deployment
- AI-optimized performance for real-time control and predictive maintenance
- Reduced environmental footprint and streamlined permitting
- Feedwater flexibility – including geothermal brines, battery recycling, and produced water sources
EC2 is a containerised solution, designed to be modular, and adaptable to a broad range of source inputs, enabling it to meet evolving industry demands. It is designed for brine-based lithium extraction, including both geothermal and solar sources, and is capable of handling a wide range of concentrations.
The EC2 process explained
Feed brine is fed into the Extract stage, where synthesised resins and novel membranes optimise lithium extraction beyond industry norms. Two streams are fed to the next stage: A Li-rich stream reaches ‘Generation II’ levels and the richest lithium stream possible for maximum downstream efficiency; and a second Li-lean stream.
These two streams flow into the Concentrate stage, where they flow through different CRFO paths: CFRO I receives the Li-rich stream where it is refined further to levels sufficient to convert to battery-grade. This stream flows to the Convert stage, while CFRO II receives the Li-lean stream and reduces total dissolved solids to below regulatory limits, allowing expedited permitting and discharge ready water.
In the final Convert stage, the highly concentrated lithium stream from CFRO I is precipitated into a solid using chemical or electrochemical processes to produce battery-grade lithium carbonate or lithium hydroxide output.
How does counterflow reverse osmosis work?
Counterflow reverse osmosis works by adding a counterflow on the permeate side of the membrane to reduce the osmotic pressure. By doing so, it reduces the amount of pressure needed to move concentrate from the feed side to the permeate side, across the salt-rejecting membrane.
The counter stream is diluted by permeate moving through the membrane and leaves the system with a higher mass flow rate and reduced concentration.
Commercial agreement justifies extraction technology
Anurag Bajpayee, CEO of Gradiant, told media: “We now have a fully operational lithium production asset in the U.S. that proves what EC² can deliver. This isn’t a concept, it’s a live facility demonstrating that clean, domestic lithium production is both viable and scalable.”
He added: “This strategic investment in the Marcellus Shale, which could supply 50% of U.S. lithium demand, validates the maturity of alkaLi’s technology and secures a long-term domestic supply.”
The facility is already proving viable with alkaLi signing a multi-year agreement with a US-based lithium-ion battery manufacturer for electric vehicles and energy storage systems to supply up to 5,000 metric tonnes of battery-grade lithium carbonate annually.