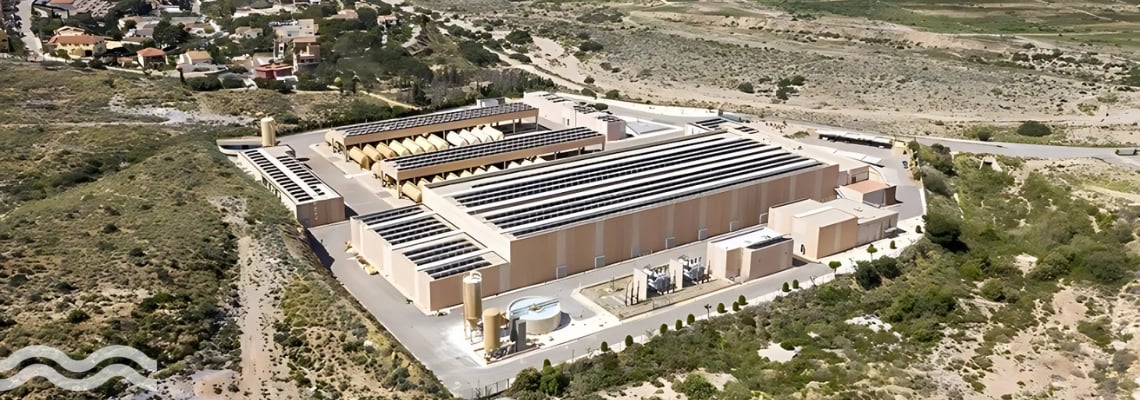
Switzerland-based optimisation specialist Sulzer is offering a service that helps to unlock operational, environmental and financial performance improvements from centrifugal pumps across a range of energy intensive industries and applications, such as desalination plants.
Creating a best practice standard for centrifugal pumps
The service is designed to create a best practice standard in energy efficiency and carbon reduction for the operation of centrifugal pumps across their lifecycle for energy intensive industries such as power generation, oil and gas, chemical, and water desalination. Pumps account for 20 per cent of the world’s total electricity demand, which means operational efficiencies have the potential to translate into significant energy and, therefore also, cost savings.
Inefficient and unreliable pumps cost operators in the industrial sectors millions of dollars in unnecessary downtime, energy costs and carbon emissions.
Building on the company’s long history and expertise in engineering, the Sulzer Energy Optimization Service combines digital analysis, machine learning and monitoring to ‘drive down carbon emissions, enhance reliability, and reduce energy costs’, all through better efficiencies in pump operation.
Ravin Pillay-Ramsamy, services division president at Sulzer told media at the launch: “Inefficient and unreliable pumps cost operators in the industrial sectors millions of dollars in unnecessary downtime, energy costs and carbon emissions every year. Sulzer Energy Optimization Service offers a comprehensive solution that tackles this inefficiency – from identification through to improvement and monitoring.”
He added: “A pilot customer in Spain will now save €1 million in energy costs and over 2,300 tonnes of carbon dioxide a year as a result of energy optimisation improvements identified by the service. By re-rating five pumps, energy efficiency increased from 72 per cent to 83 per cent saving the operator 5,000 megawatts per hour in electricity every year.”
According to Sulzer, a one per cent increase in global pump efficiency would save around 59 terawatts per hour of electricity – which is equivalent to New Zealand’s annual power needs. The company also believes that the efficiency of some pumps across the industries the service is designed for could be increased by as much as 20 to 30 per cent.
(Credit: Sulzer)
Four steps to optimised pump operation
The optimisation process takes place over four steps:
First, there is an initial energy audit identifies areas of inefficiency using Sulzer’s proprietary calculator – PumpWise. This outlines potential energy, carbon and monetary savings.
Next, a tailored proposal is generated by Sulzer’s team, which presents a range of options that will enable the pump to run at its best efficiency.
This takes place through an engineered retrofit using a range of techniques such as hydraulic re-rates, specialised coatings, wear clearances, and more. Each option weighs operational costs, investment, downtime, payback, and efficiency guarantees.
The chosen upgrades are then implemented with support from Sulzer’s retrofit team which has delivered more than 4,000 retrofit projects globally since its setup in 2010. The team is supported by a network of more than 120 service locations globally.
Following the retrofit optimisation, the company offers a performance agreement to maintain optimised reliability and efficiency. This includes access to Blue Box, which is Sulzer’s proprietary machine learning technology that turns pump performance data into actionable insights.
Reducing global pump energy demand
Pillay-Ramsamy explained the value further: “For operators who are constantly challenged to do more with less, making energy efficiency improvements is a win-win. With pumps accounting for 20 per cent of the world’s electricity demand, we want to offer a streamlined, futureproofed way for customers to improve their energy efficiency regardless of their pump OEM.”
He added: “To do so, we’ve combined the competence of our people and longstanding engineering expertise with our proprietary innovations and wrapped them in a collaborative and customer-centric approach. Altogether we believe this solution creates a new best practice standard for pump operation that goes above and beyond in supporting operators to remain future-ready.”
Reinvigorating a mothballed desalination plant
The service has been used for a number of case studies, including a desalination plant in Spain that had been mothballed for 12 months due to high energy costs of the pumps. The solution was to re-engineer the pumps to achieve optimum efficiency (in this case, 10 per cent efficiency savings), while at the same time reducing the number of filtration stages to lower the demand on the pumps. Other improvements included new pump casings, crack repairs, and a new rotor.
After rigorous testing, all five pumps operated at their best efficiency point with less energy required. Cost savings from the optimised plant will be used to offset some of the costs of a new solar plant that will be used to power the desalination plant.
Annually, the pumps are expected to consume 5 megawatts less power than in their original state, with an associated carbon reduction of 2,345 tonnes. Operational expenses are estimated by the company to reduce by €1 million a year.
Water produced by the plant will be used to irrigate 3,000 hectares of agricultural land each year and provide 20 cubic hectometres of water per year to the local population.
Share your water technology stories with us
Do you have an innovation, research results or an other interesting topic you would like to share with the international water technology industry? The Aquatech website and social media channels are a great platform to showcase your stories!
Please contact our Sr Brand Marketing Manager Annelie Koomen.
Are you an Aquatech exhibitor?
Make sure you add your latest press releases to your Company Profile in the Exhibitor Portal for free exposure.